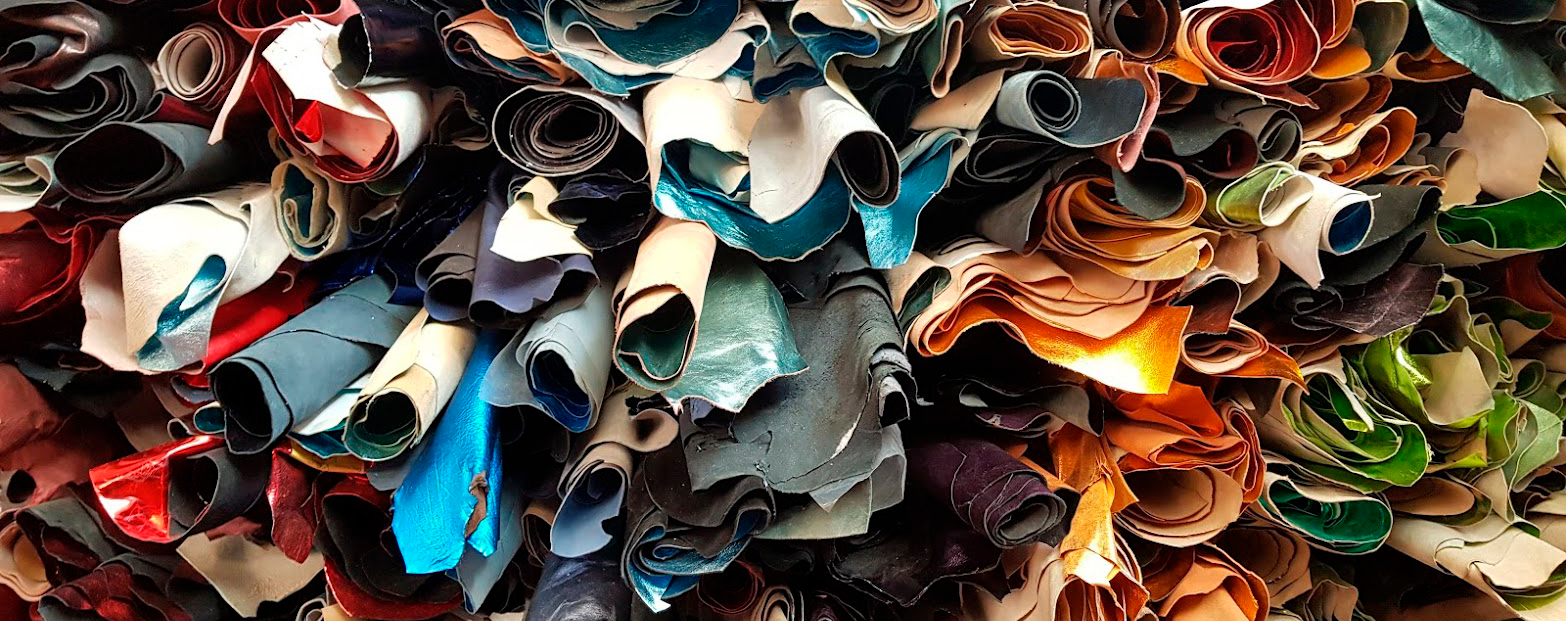
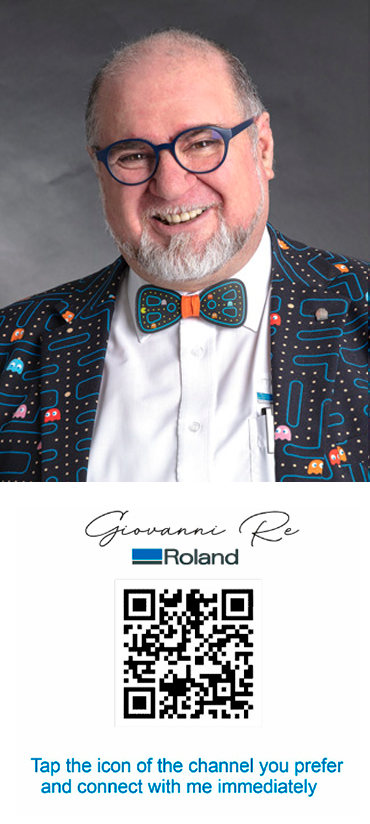
Giovanni Re
Roland DG Mid Europe アカデミースペシャリスト
モデリングマシン、スキャナー、3Dプリンター、カッティングプロッター、大判プリンター、彫刻機、レーザー彫刻機などのあらゆるデジタル機器に精通し、2003年以来、ローランド ディー.ジー. アカデミーにて1万人以上のユーザートレーニングに携わり、デジタルファブリケーションの魅力を発信し続けている。イタリアのコミュニティ「Artigiano Tecnologico」(技術職人)の創設者として、ビジュアルコミュニケーションとデジタルクラフトマンシップの分野における研究、トレーニング、文化的普及に取り組み、TEDxをはじめとする数百のイベントにも登壇。その活動域は大学、ファブラボ、さまざまな教育機関に及ぶ。また、書籍「#CommunityManager」の著者、wow-meter(ワオメーター)の発明者、IoT Visual Interactive Communicationの創設者でもある。
モットーは「知る、やる、やり方を知る、人に知らせる」。
Giovanniの活動は、www.giovannire.blogspot.itでフォローできます。
写真の下にあるQRコードで、彼のソーシャルメディア・アカウントもアクセスしてみてください。
近年、バッグや靴、衣服などの革製品に個性的でアーティスティックなグラフィックを施したり、名前などを入れるケースが増えています。この傾向はグッチやルイ・ヴィトンのような高級ブランド品から、カジュアルな身の回りの小物類にまで広がり、デザインの多様化やパーソナライズと呼ばれるトレンドとして大きな注目を集めています。こういった革製品への加飾・プリントが身近になった要因のひとつとして、UVインクジェット技術に代表されるデジタル印刷の進化があります。今回は革へのデジタルプリント手法についてご紹介します。
さて、せっかくの機会ですので、本題に入る前に、まず動物の原皮からどのようにして革製品が作られるのか、イタリアで有名な「なめし工程」を説明したいと思います。
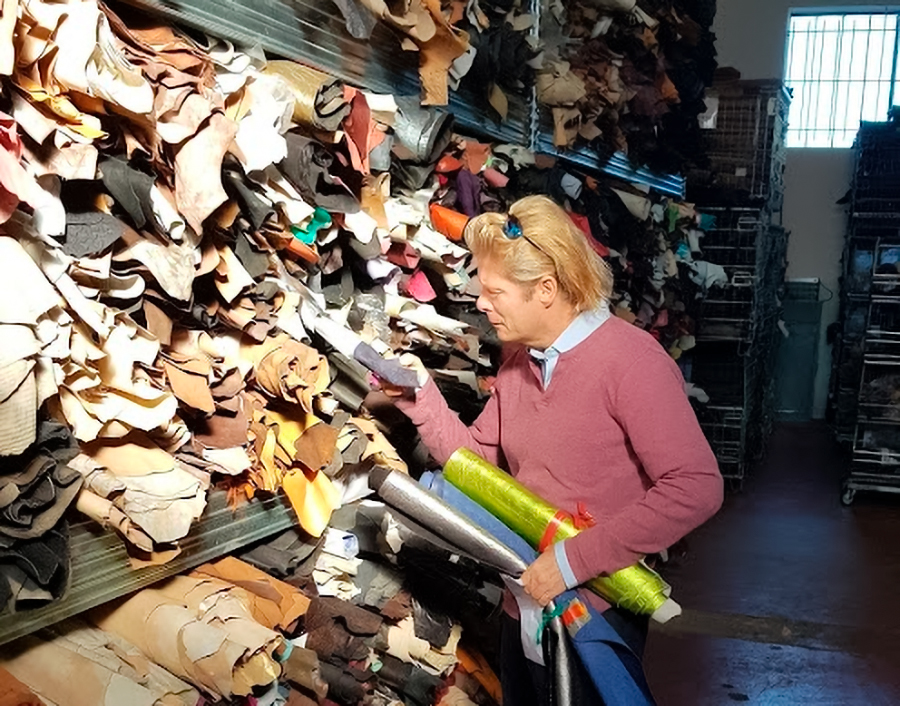
革のなめし工程
イタリアは高品質ななめし革の生産で有名で、ヴェネト州、トスカーナ州、カンパニア州、ロンバルディア州などに約1,200のタンナー(なめし工場)と17,000人以上の従業員を擁し、この産業の世界的なリーダーとして知られています*1。 古代の職人技に由来する皮革の製造工程は、時に非常に長く、アパレル、靴、鞄、家具、さらには自動車製造の世界に向けて、多様な製品を提供しています。製造工程では化学的な方法が用いられ、その方法は、どんな種類の皮を使い、何を作るかによって異なり、職人たちの長い経験から得られた技術の蓄積の上に成り立っています。各タンナーにはそれぞれ受け継がれてきた独自のレシピがあり、その工程は他に類を見ないユニークなものとなっています。
*1 出典: UNIC, ECONOMIC PERFORMANCE ITALIAN TANNING INDUSTRY, 2019
前工程
まず、皮を本体から分離した後、腐敗を防ぐために塩漬けにする必要があります。次に、皮に水分を含ませて元の湿度に戻す「水漬け」という作業を行います。「脱毛」は、原皮から毛を取り除くためのもので、毛を化学的に溶かして銀面と呼ばれる表皮から分離させる方法がとられます。ここで行われる「石灰漬け」は、原皮に含まれる繊維質を膨潤させてほぐし、なめし剤を浸透しやすくするための準備でもあります。原皮に厚みがある場合は、オプションとして皮全体の厚みを均一にするための「分割」と呼ばれる工程が入ることもあります。
次に、「脱灰(だっかい)」、「酵解(こうかい・ベーティング)」、「脱脂(だっし)」という重要な工程に移ります。「脱灰」では革の繊維に残っている石灰分を取り除き、「酵解」では革の繊維をリラックスさせ滑らかにし、浸透性も高めます。最後の「脱脂」では皮の自然な脂肪分を減らしたり、なくしたりすることで、その後のなめし工程での化学製品の吸収を促進します。そして、長期間の保存を可能にするために、皮のpH値を7から4程度に下げる(酸性にする)「浸酸(しんさん・ピクリング)」という工程に入ります。これは、酵解作用を完全に止めるためにも必要です。
なめし
そして、皮を「革」に変化させる主となる加工工程が「なめし」で、湿度や温度、薬品への耐性を与えるために行われます。クロム、植物タンニン、アルミニウム、ジルコニウム、アルデヒドなどのなめし剤を使い分ける、職人のあらゆる知識が必要とされる工程です。
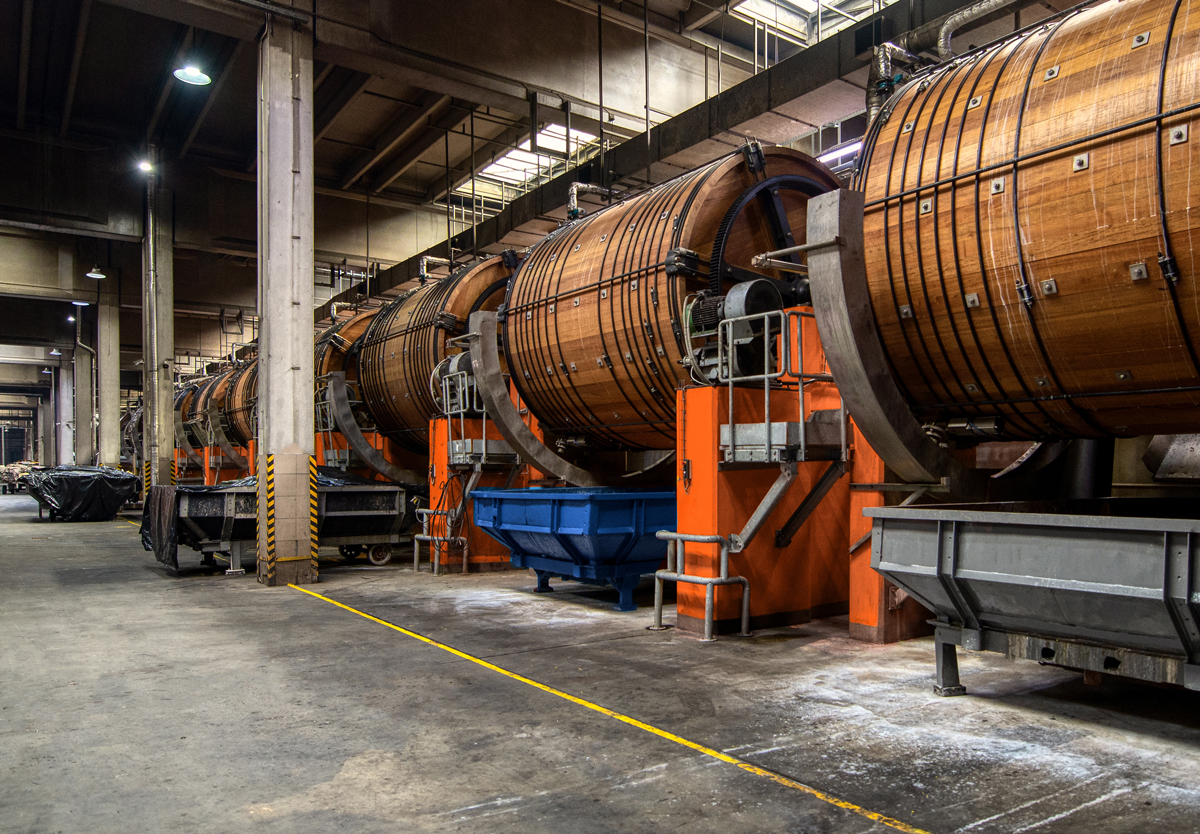
後工程
なめした後の革はシリンダーでプレスして、吸収した水分を減らし、全体的にならします(「水絞り」)。オプション工程として、革全体の厚みを均一にするための「革漉き(かわすき)・シェービング」や、「分割」をこのタイミングで行う場合もあります。革漉き工程はフラットベッド式のプリンターに設置する際の平坦性を確保するため、革へのプリントを施す場合にとても重要な工程です。
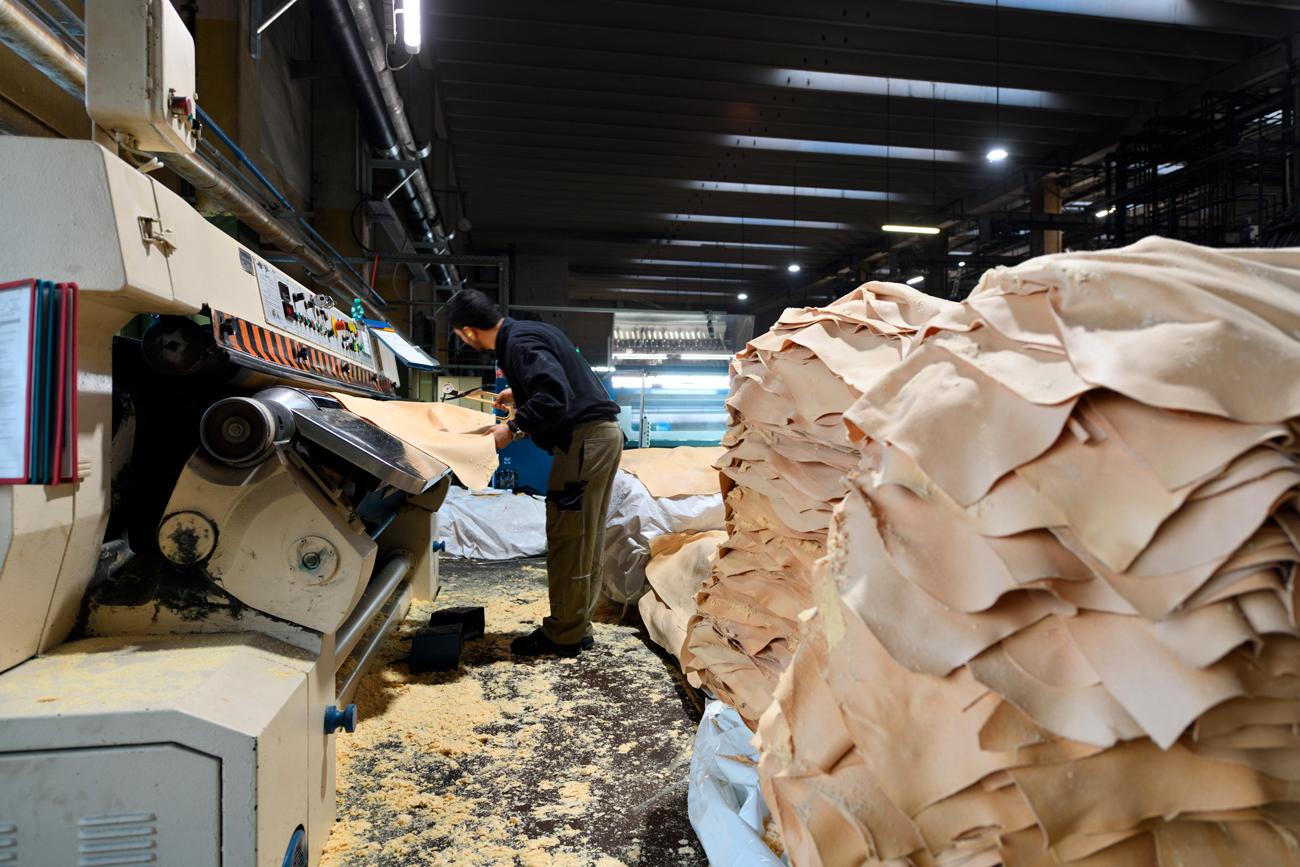
さらに、「再なめし」をすることで、革に柔らかさや、耐汗性を与えるなど、用途に応じて革製品に付加機能を与えることができます。再なめしは、専用のドラムに用途に応じたなめし剤を投入し行われます。
次に、天然または人工の多様な着色料を使用して革に色をつける「染色」工程です。ここでは、「加脂」という工程もあり、革に柔らかさと疎水性(耐水性)を与えますが、使用する植物油や動物油が印刷工程で使用するインクと相容れない可能性があるため、あらかじめ考慮が必要です。この時点での革はまだ水分を含んでいるため、さらに「乾燥」という工程が必要です。ここでは、完成した革を真空熱板の上に置いたり、空中のチェーンに吊るしたりして乾燥させます。
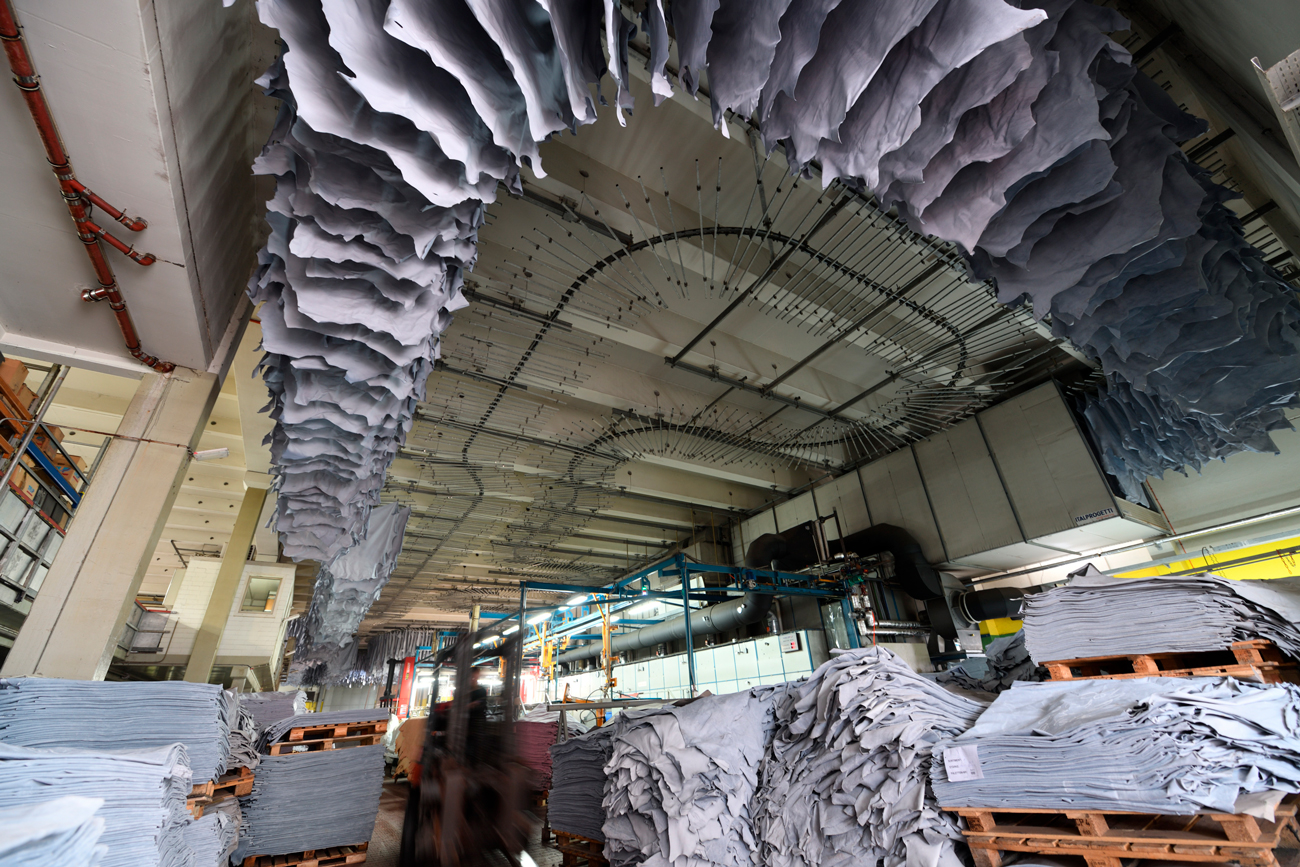
革の後加工サイクルはまだ終わりません。「仕上げ」は、光沢、硬さ、弾力、汚れ・水・傷への耐性など、製品を特徴づけるための一連の作業です。この段階では、スプレー塗装、ニス塗り、パディング(手塗り)など、さまざまな化学的・機械的処理が行われます。これらの工程が終わると、トリミング、採寸、梱包へと進みます。
加工・仕上げによる革の種類
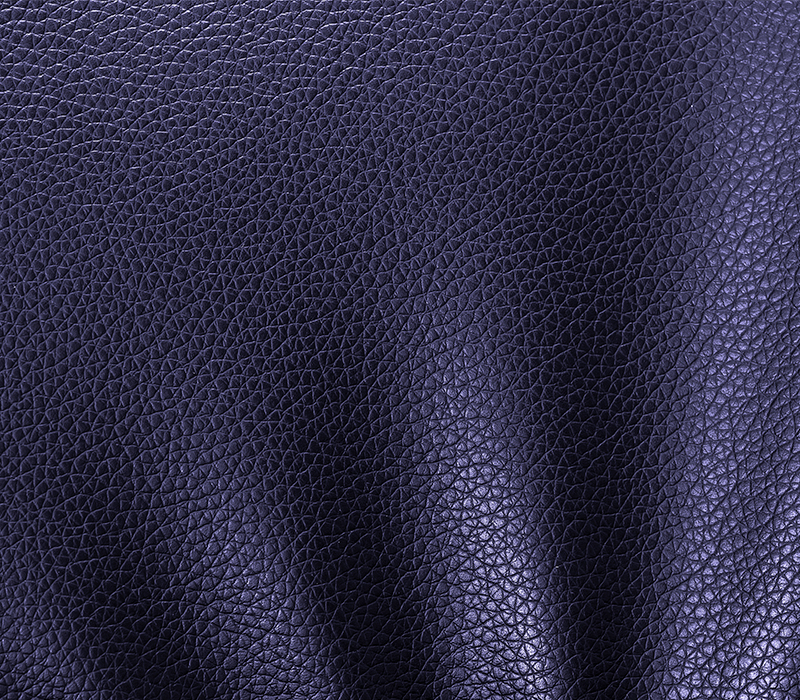
シュリンクレザー: 乾燥したドラムの中で回転させることで、シボの質感がより鮮明になった革。
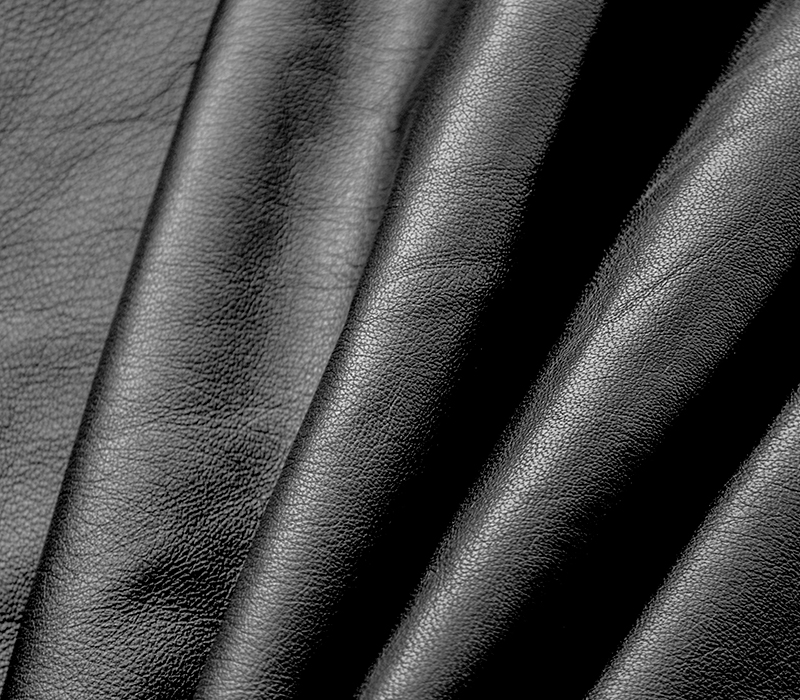
ナッパ: 柔らかく丈夫なフルグレイン(銀付き)レザー。
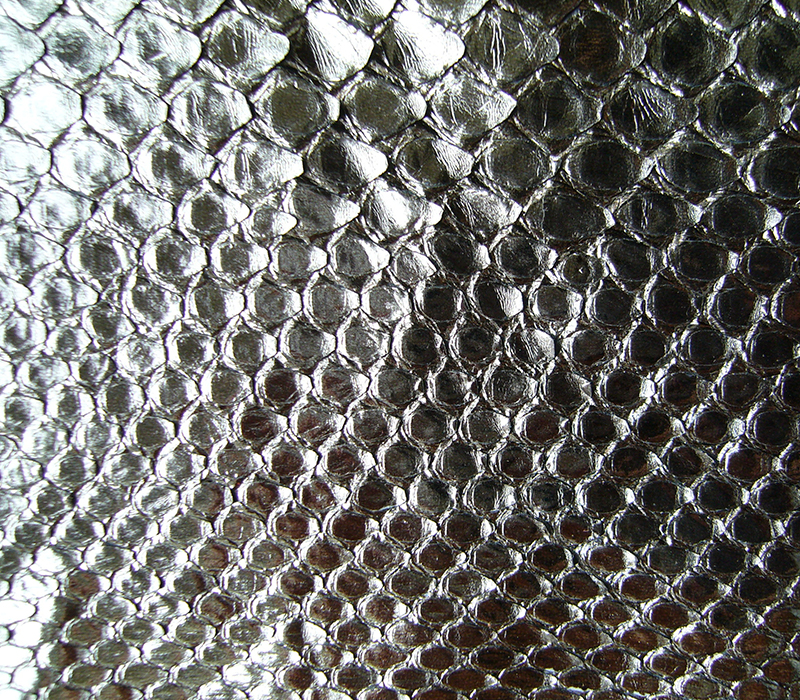
ラミネート加工: フィルムや箔でメタリックな風合いを出した革の加工。
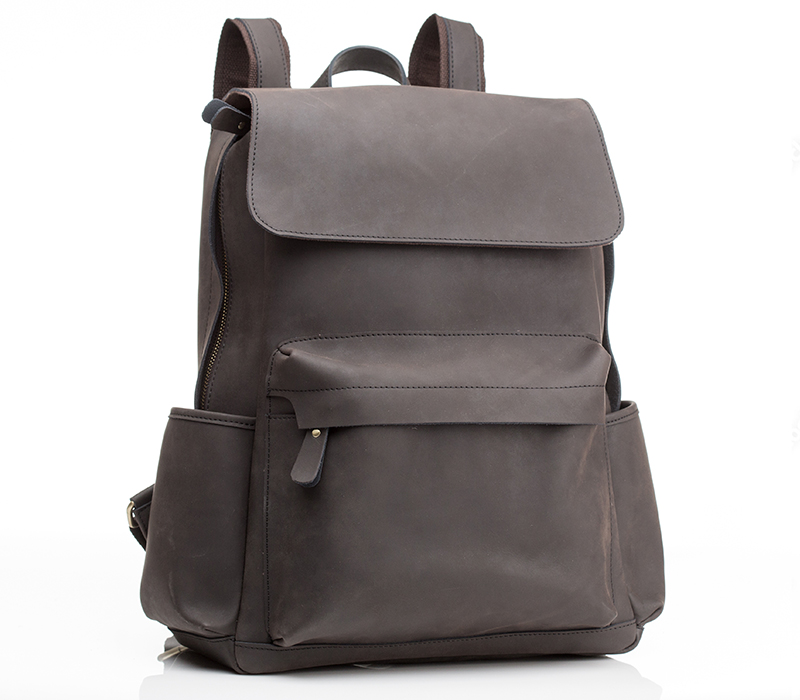
ヌバック: 革の銀面(表面)をバフィング(やすり)し、起毛させた革。銀面が完全になくなるわけではなく、ある程度視認できる状態。
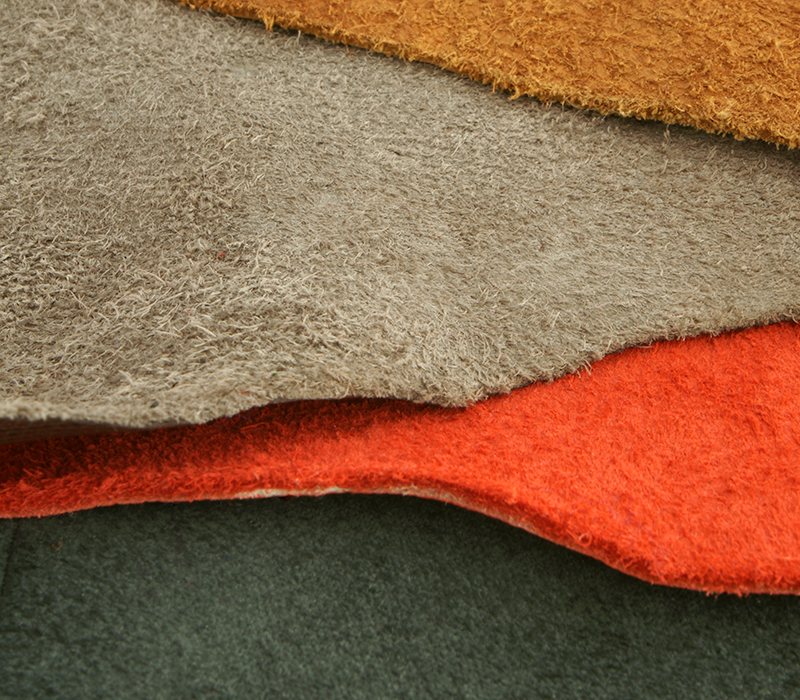
スエード、ベロア: 革の床面(裏側)をバフィングし、起毛させた革。床面を仕上げることで、ヌバックよりも繊維が長く粗めになる。

タンポナート: 仕上げ剤を染み込ませた綿を使って職人の手作業で仕上げた革で、ツートーンに染色したり、異なる色調の光沢効果が付加される。
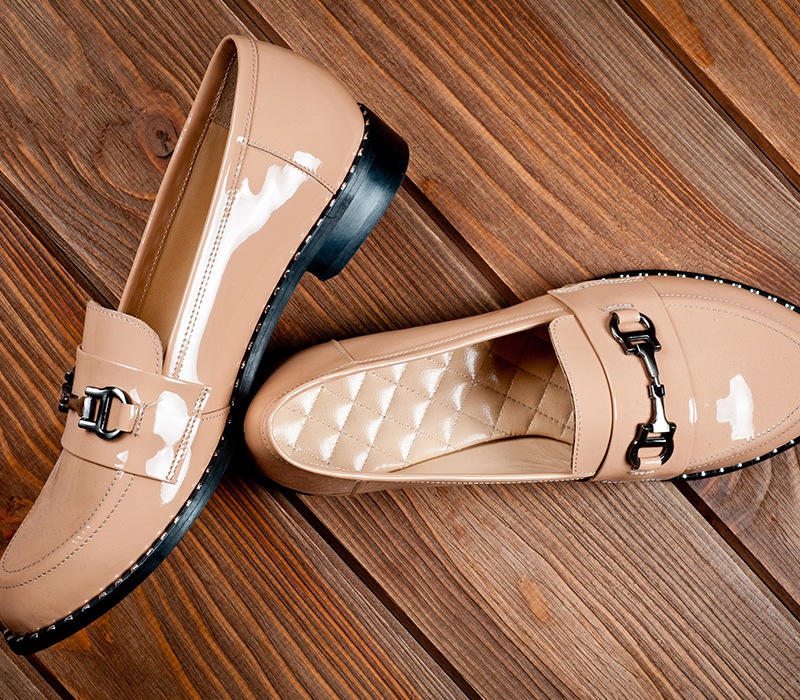
エナメル、パテントレザー: 革にラッカー塗装を施し、光沢感を演出。
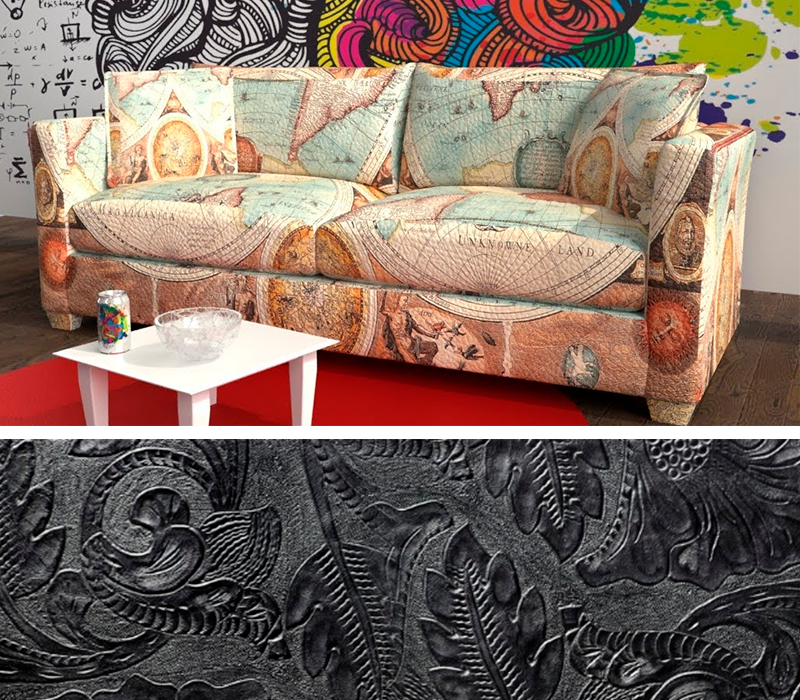
プリント革: レリーフプリントと呼ばれるエンボス加工、スクリーンプリント、デジタルプリントなど、さまざまな技法で表面にプリントされた革。
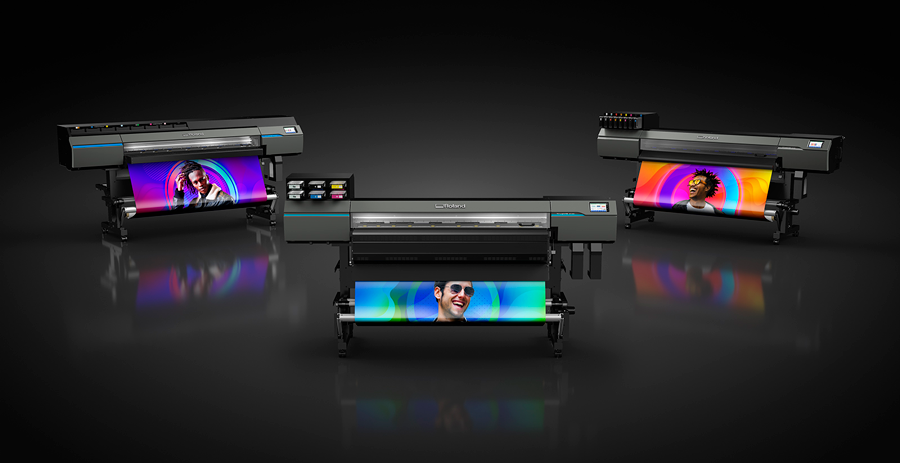