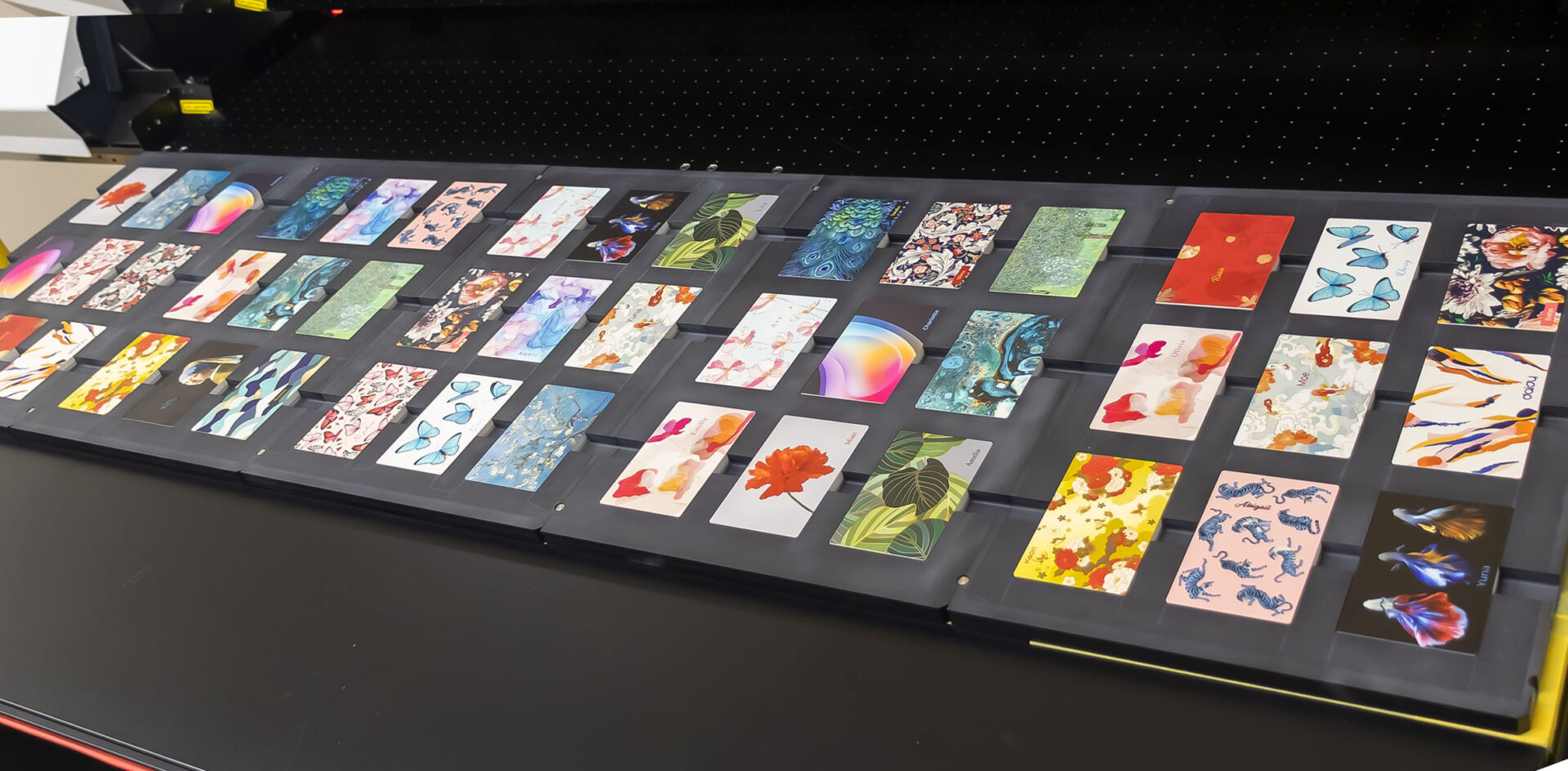
ダイレクトプリントで実現するマスカスタマイゼーション
マスカスタマイゼーションという言葉をご存じでしょうか。大量に生産するモノづくりの方式は、マスプロダクションと呼ばれています。一方、顧客一人ひとりのニーズに合わせて商品やサービスを最適化する戦略を、カスタマイゼーション、あるいはパーソナライゼーションと呼びます。商品の色合いを自分好みに仕立てる事ができたり、自分の体の寸法通りに服をオーダーしたり、自分の名前を印字してもらったりするサービスがこれにあたります。そして、この二つの相反する言葉が組み合わさったのが、マスカスタマイゼーションです。生産性は高く維持しながら、顧客の個々の好みを商品に反映させる生産方式で、実際に世の中にはオンラインサイトで自分好みにスニーカーやスポーツウォッチをデザインしてオーダーできるサービスなども存在します。
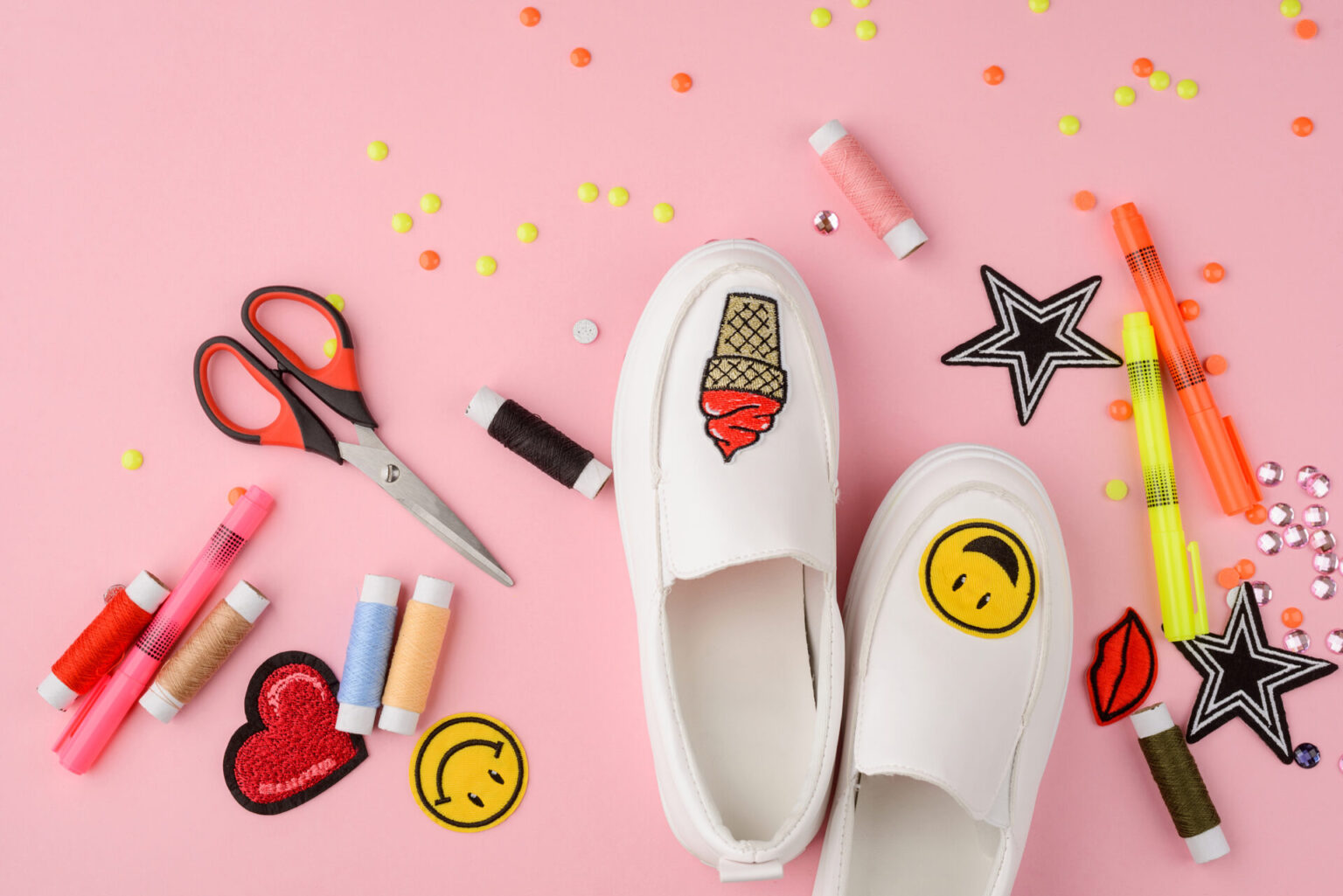
今回の記事では、マスプロダクションで生産された化粧パレットケース一つひとつに、個別の名入れやデザインを施し、一気にダイレクトプリントすることでマスカスタマイゼーションを実現するソリューションを紹介いたします。
ソリューション概要
UV硬化インクを使用したフラットベッド方式の大判インクジェットプリンターは立体物にダイレクトに印刷ができ、印刷対象の商品やパーツをテーブル上に敷き詰めれば、生産効率を高く維持することができます。今回使用するのは、ローランド ディー.ジー.のLEC2-640に大判のフラットベッド機構を組み付けた、Mastermind社のMR-015というプリンターです。印刷対象の素材によっては、UVインクの密着性を高めるため、プリンターに搭載されているECO-UV EUV5-5PR(プライマー)インクを前処理用に印刷します。印刷した商品は、無印良品で販売されているABS樹脂製の化粧パレットケースです。ABS樹脂は比較的UVインクと相性が良いので、プライマーの前処理は必ずしも必要というわけではありません。また、印字面をスポットニスでオーバーコートすることで、擦過性を高めたり、凹凸を表現して意匠性を高めることもできます。
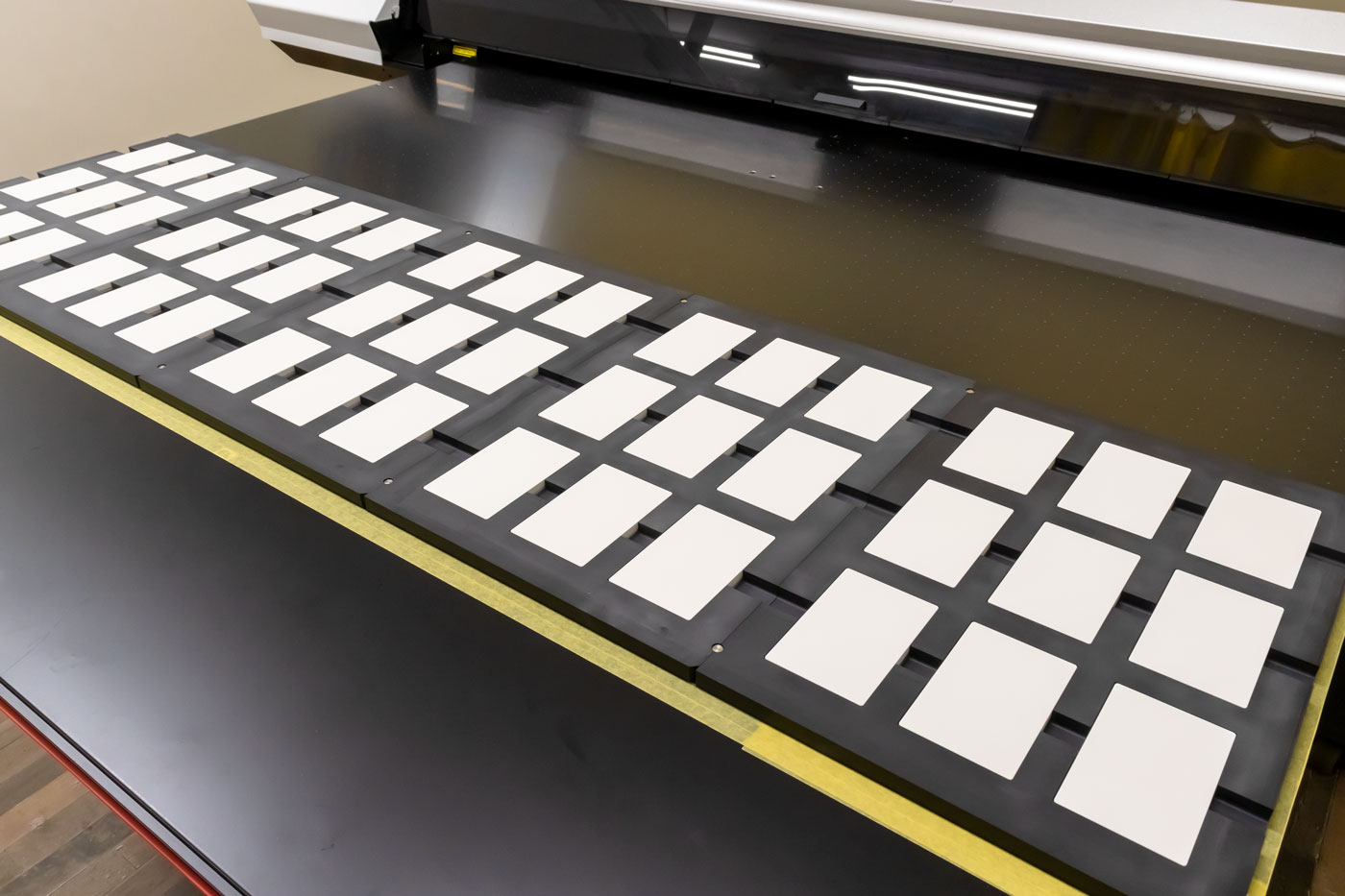
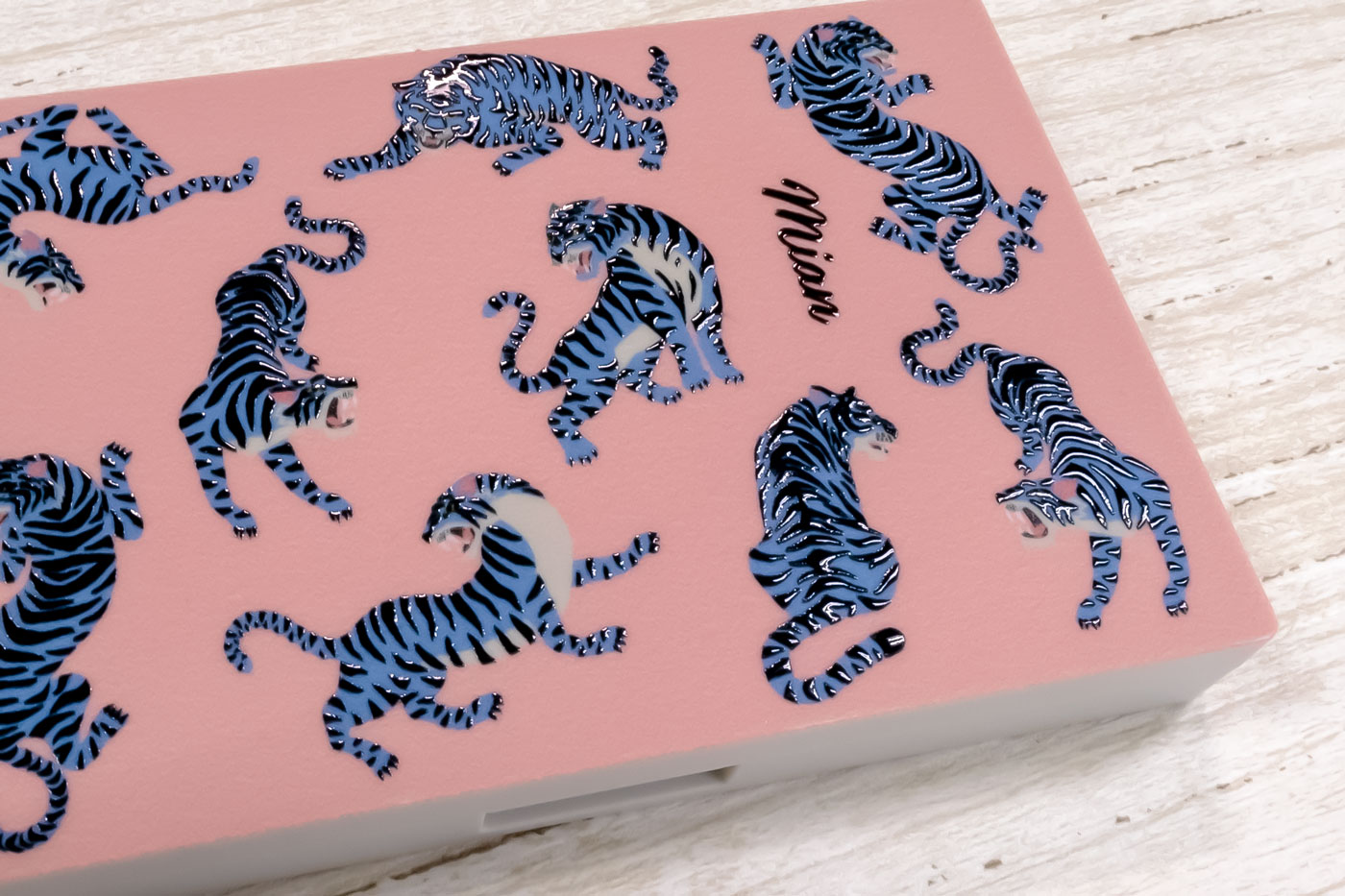
生産効率を高めるために重要なのが、印刷対象商品を毎回同じように配置することができる治具の存在です。治具があると、印刷対象となる商品をフラットベッド上に配置する位置が明確になり、商品を取り替える度に印刷位置の調整を実施する必要がなくなるため、生産効率が格段に向上します。治具は、印刷する商品の形状に合わせた切削加工することで製作できます。このソリューション事例では、切削加工による治具製作サービスを提供する、静岡県浜松市の谷﨑製作所に専用治具を準備していただきました。切削加工機があれば治具の社内生産も可能ですが、慣れないうちは外注するのも有効な手段です。
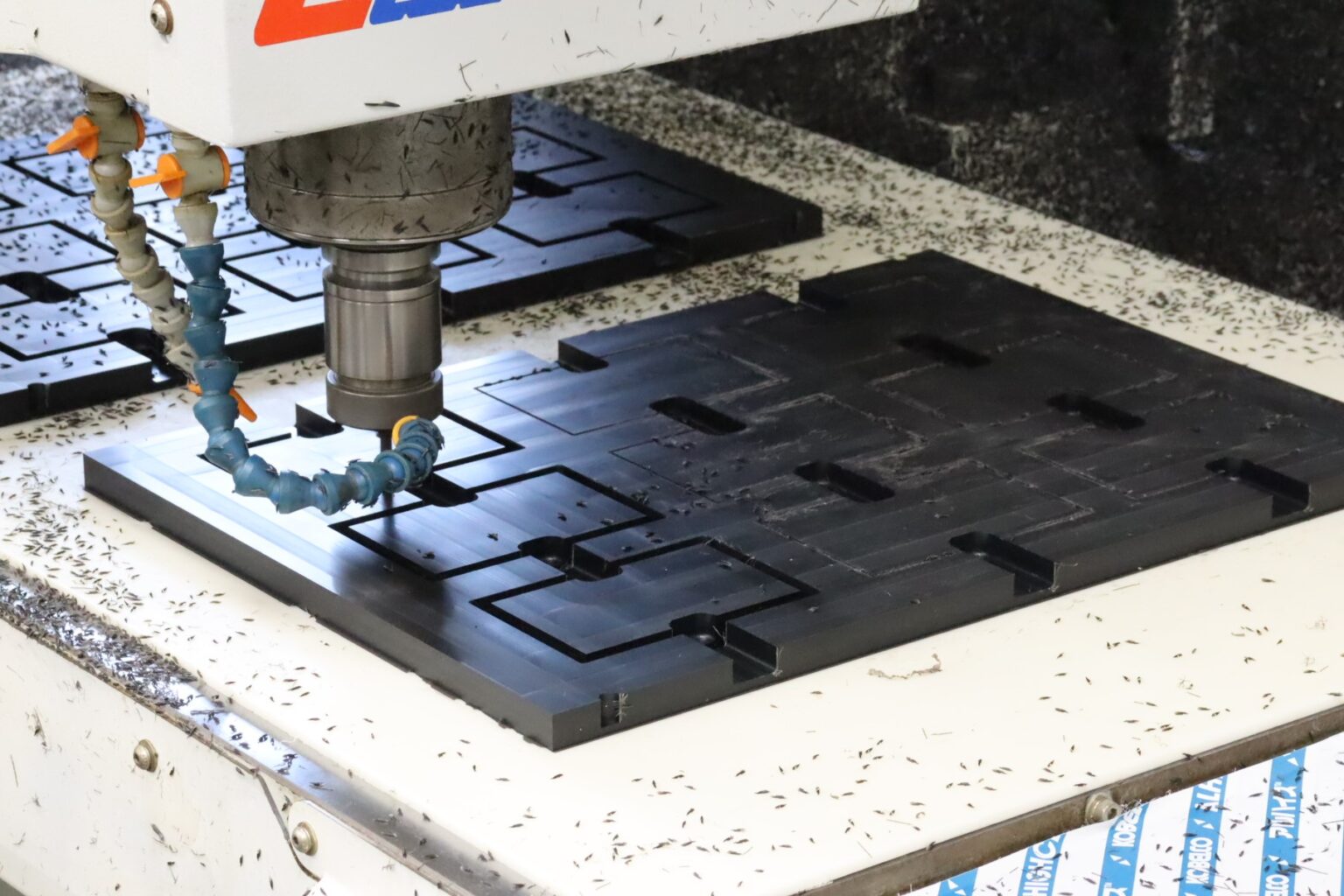
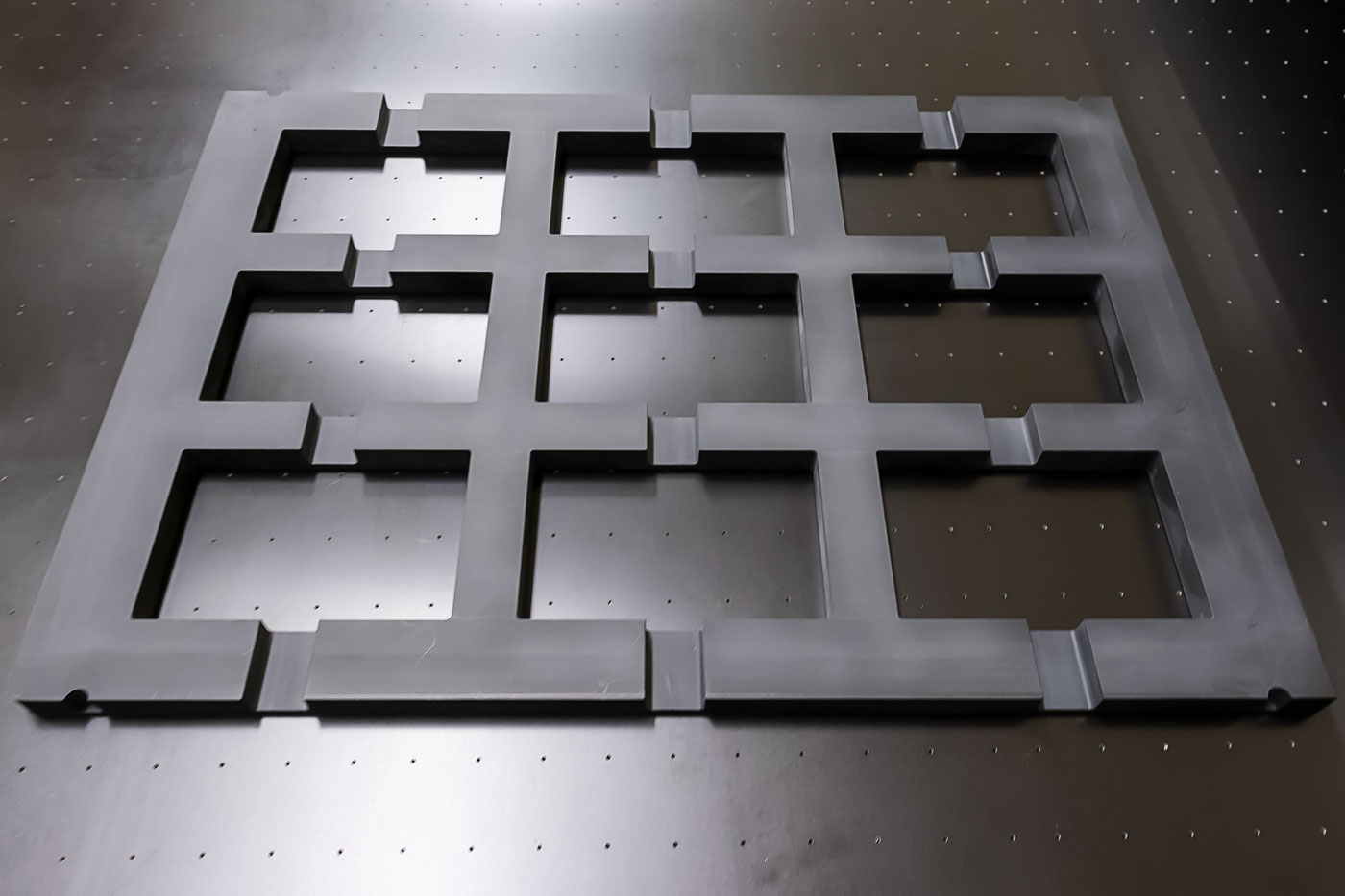
治具の切削は、印刷対象商品の形状に対して少し余裕を持たせ、取り出し口を切削しておくと運用しやすくなります。治具の厚みは、素材の厚みに対して少し薄めに切削します。治具をプリンターのフラットベッド上に設置し商品を配置します。治具の寸法通りに印刷データをレイアウトして印刷テストを行い、データ上で位置の微調整を行ったのち、印刷を実施します。
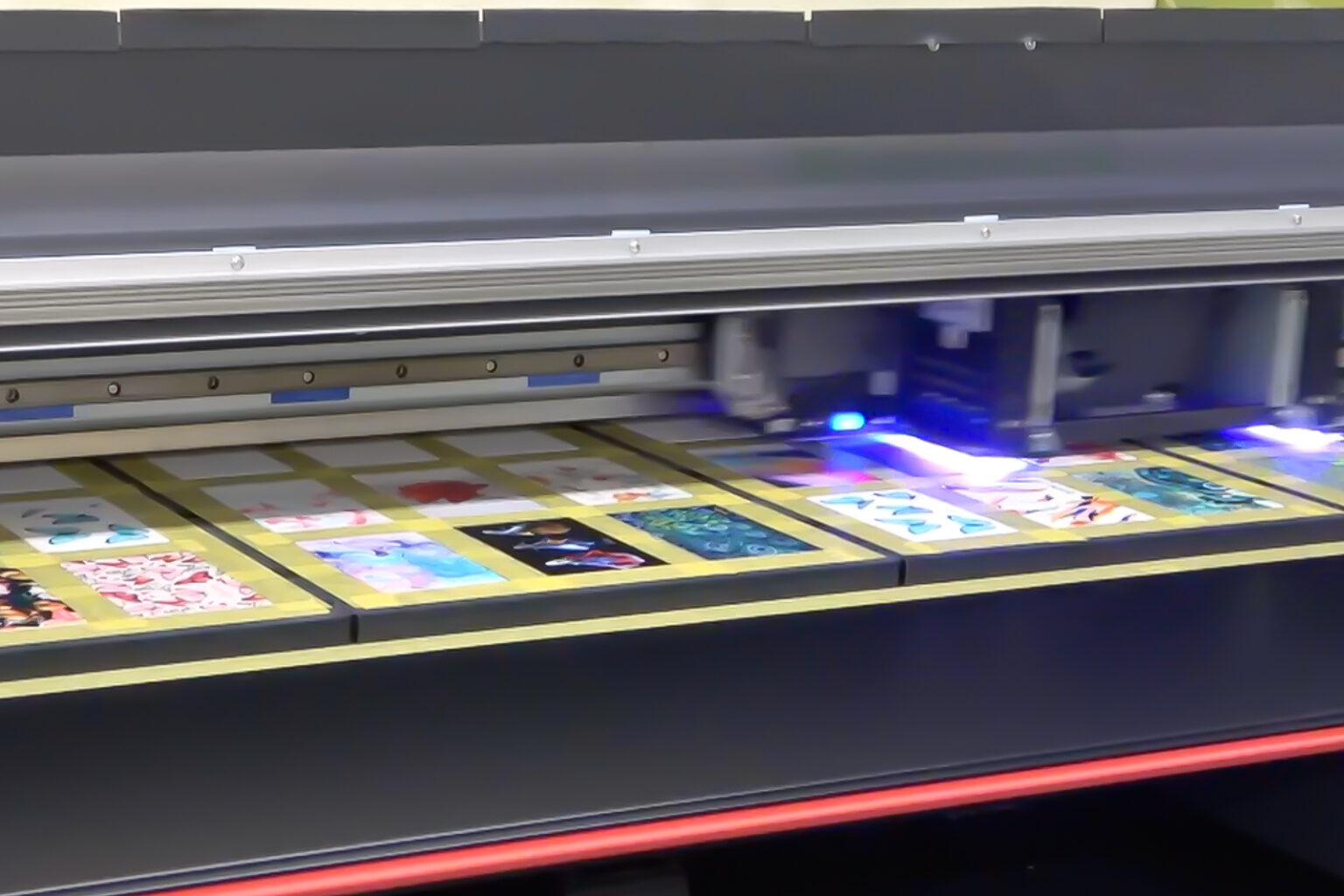
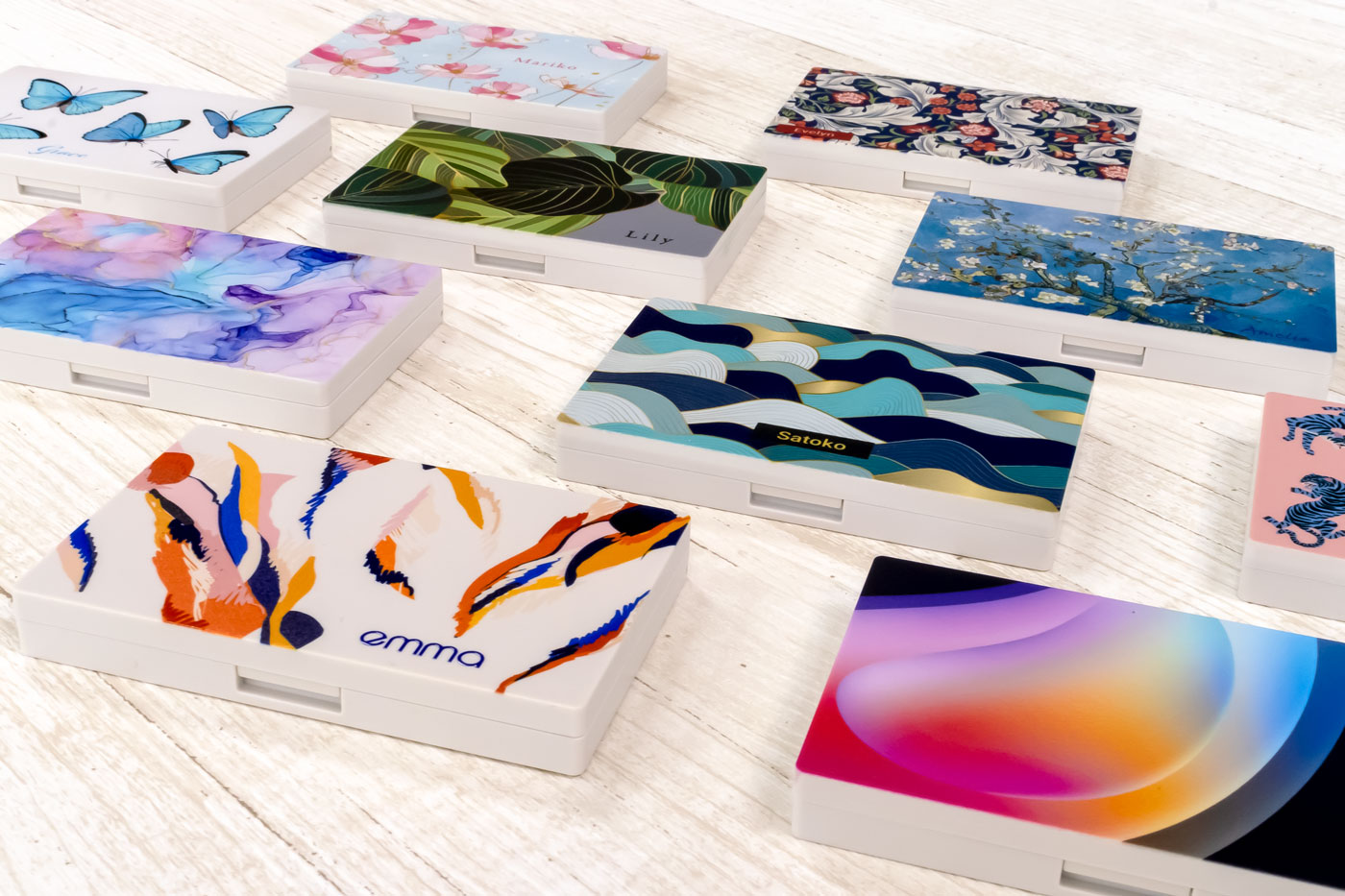
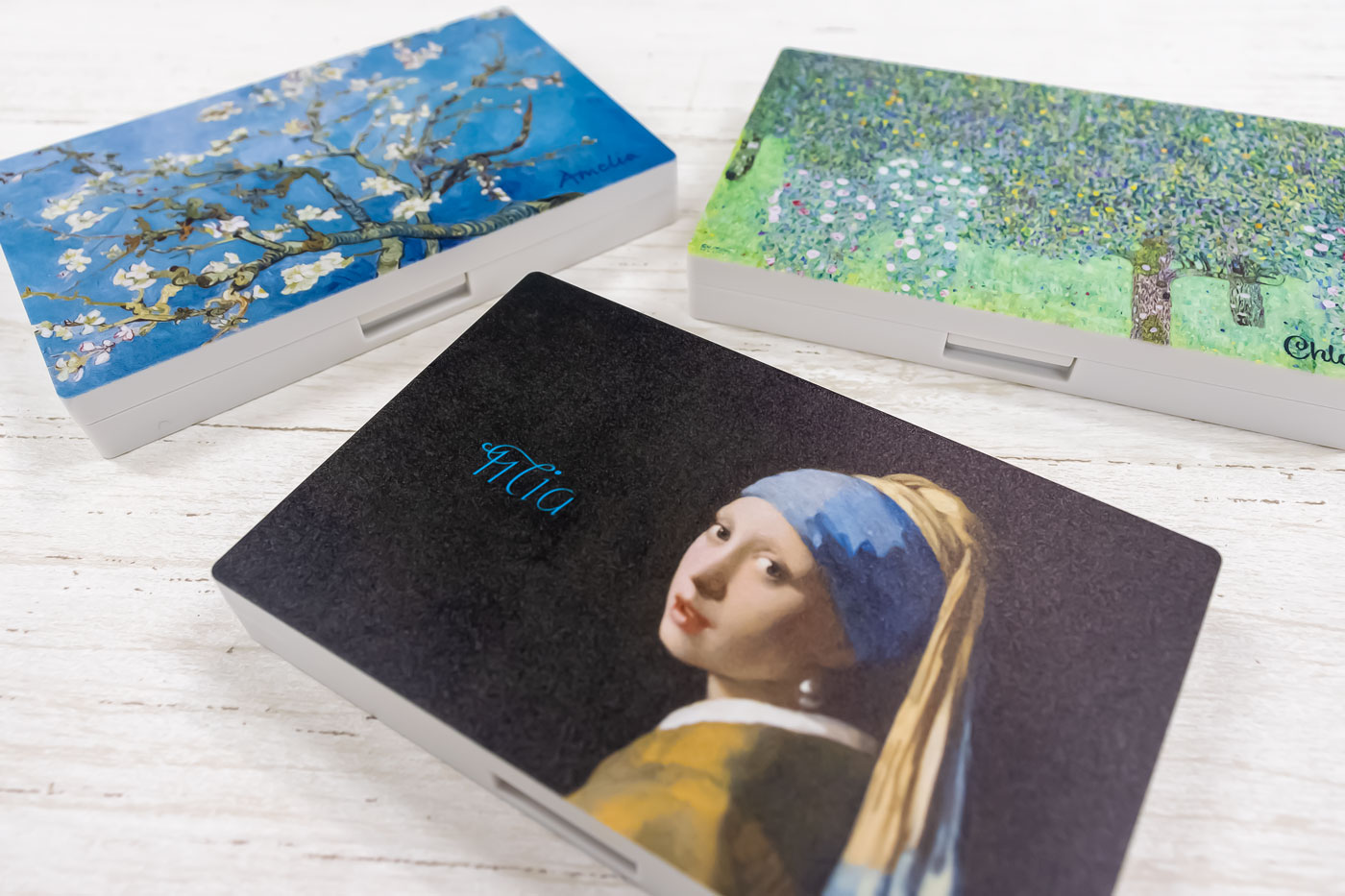
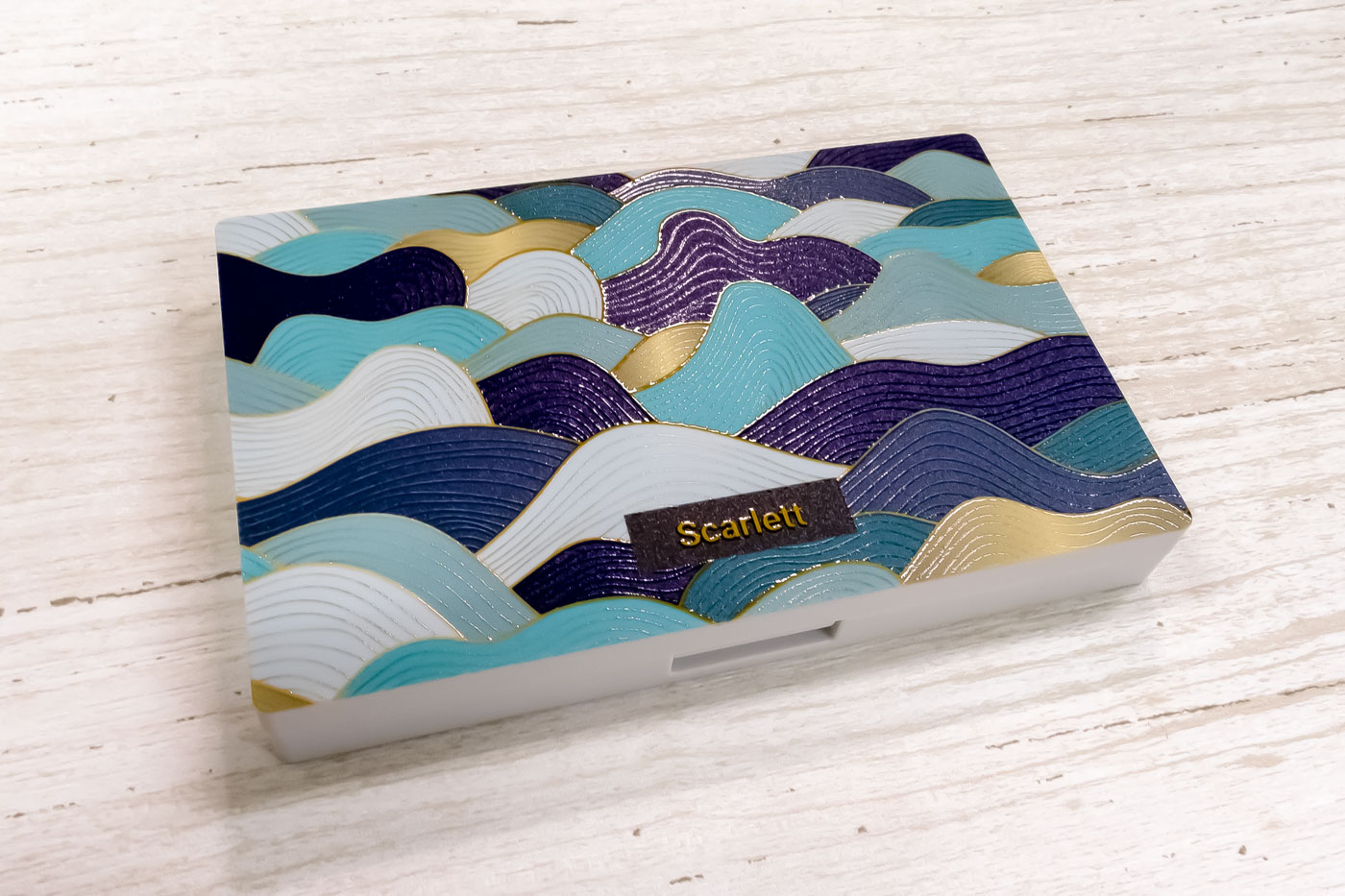
ソリューション構成
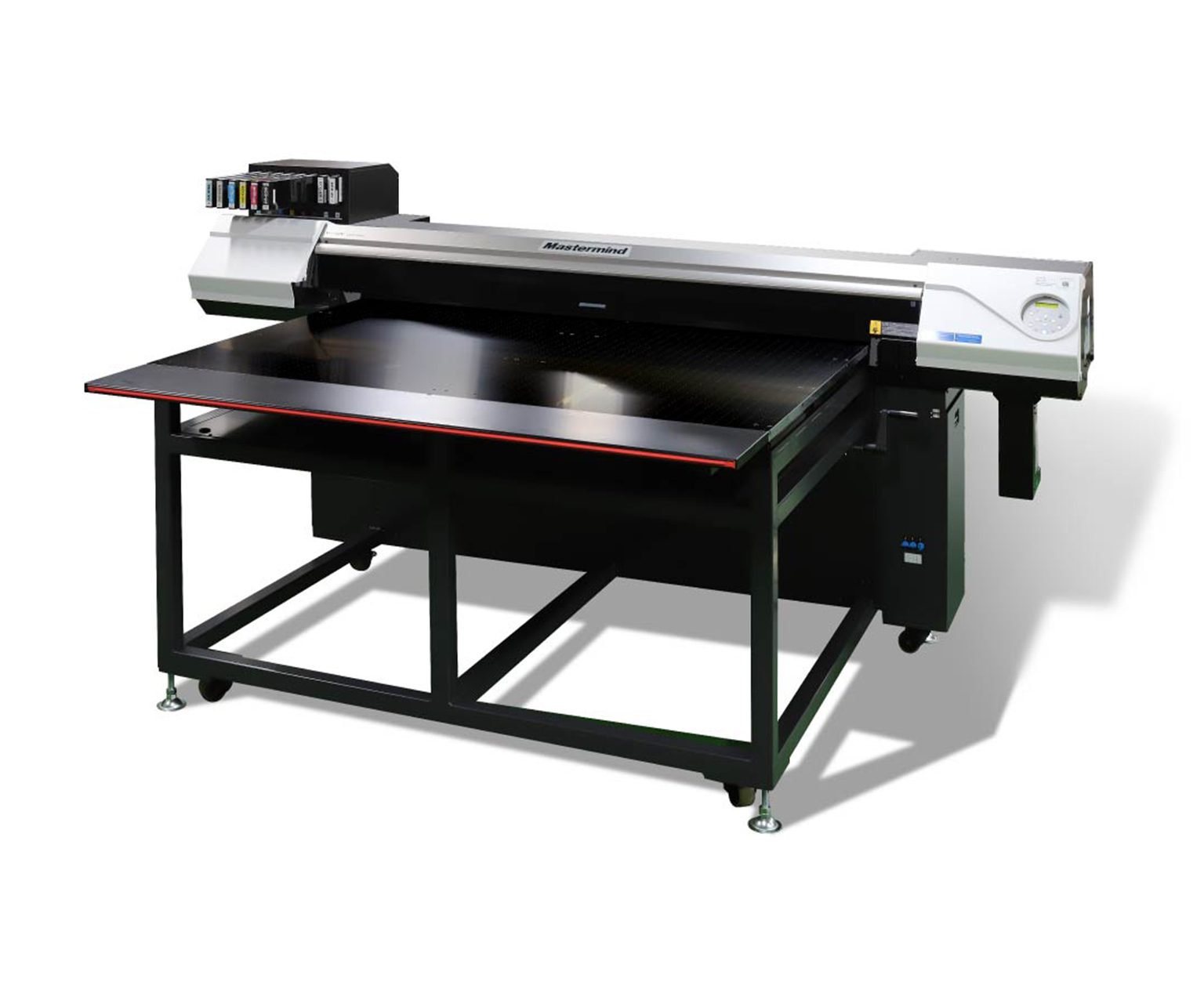
UVインクジェットプリンター Mastermind MR-015
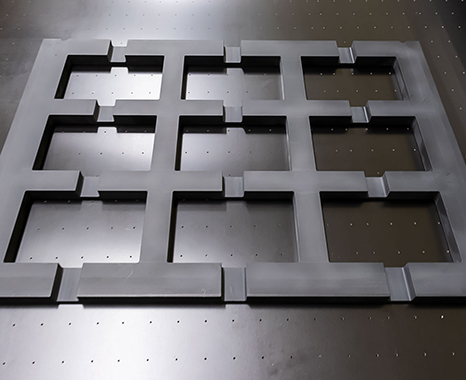
印刷治具
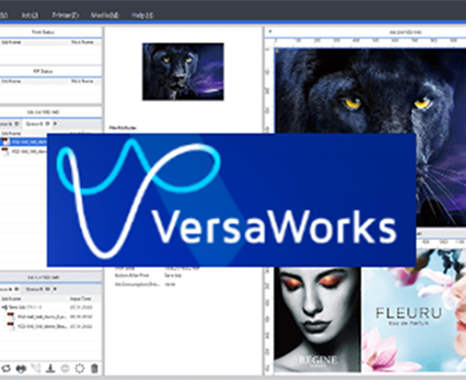
出力ソフトウェア VersaWorks 6 (LEC2シリーズに標準付属)
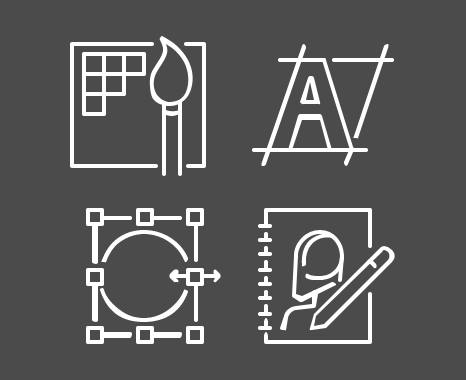
Adobe IllustratorやCorel DRAWなどのデザインソフトウェア
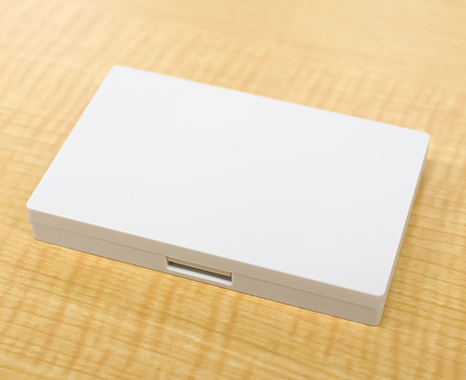
印刷対象商品(メイクパレット)
製作プロセス
-
STEP1
印刷治具の製作
印刷対象のメイクパレットの寸法で、複数個一度に印刷できる仕様の印刷治具を製作する。
-
STEP2
デザインデータ制作
印刷治具のレイアウト通りに、印刷データを準備する。
-
STEP3
印刷治具をプリンターに設置
印刷治具をUVフラットベッドプリンターのテーブル上に設置し、印刷対象のメイクパレットをセットする。
-
STEP4
印刷位置の微調整
印刷治具の上から透明シートをかぶせて印刷テストを行い、印刷位置にズレがある場合はデータ上の位置を微調整する。これを繰り返し、データ位置を確定させる。
-
STEP5
印刷
CMYKとスポットニスを印刷。
