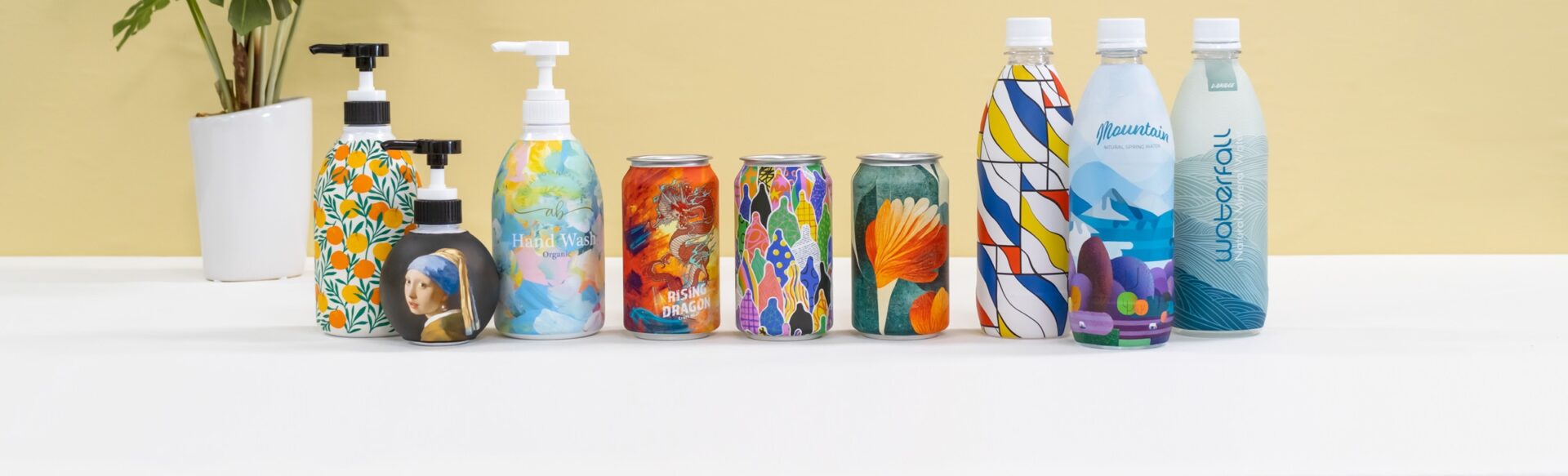
Mock-up Production of Shrink-Wrapped Packaging Using Flexible UV Ink
Shrink-wrapped packaging, which employs heat-shrinkable film that is wrapped around containers of various shapes, has been growing more popular in the beverage, food, and household product packaging fields in recent years as it allows 360-degree branding and communication of products. This labeling and packaging method is highly design-oriented and can include ingredient lists and instructions for use as well as branding information while replacing adhesive labels.
In Japan, shrink wrapping has become popular for packaging PET beverage bottles where its perforations have contributed to a high recycling rate for containers, as the practice of separating film and bottles for disposal has become widespread. In Europe and the United States, where such customs do not yet exist, new shrink films made of PET material that can be recycled together with bottles have also emerged and are becoming more environmentally friendly.
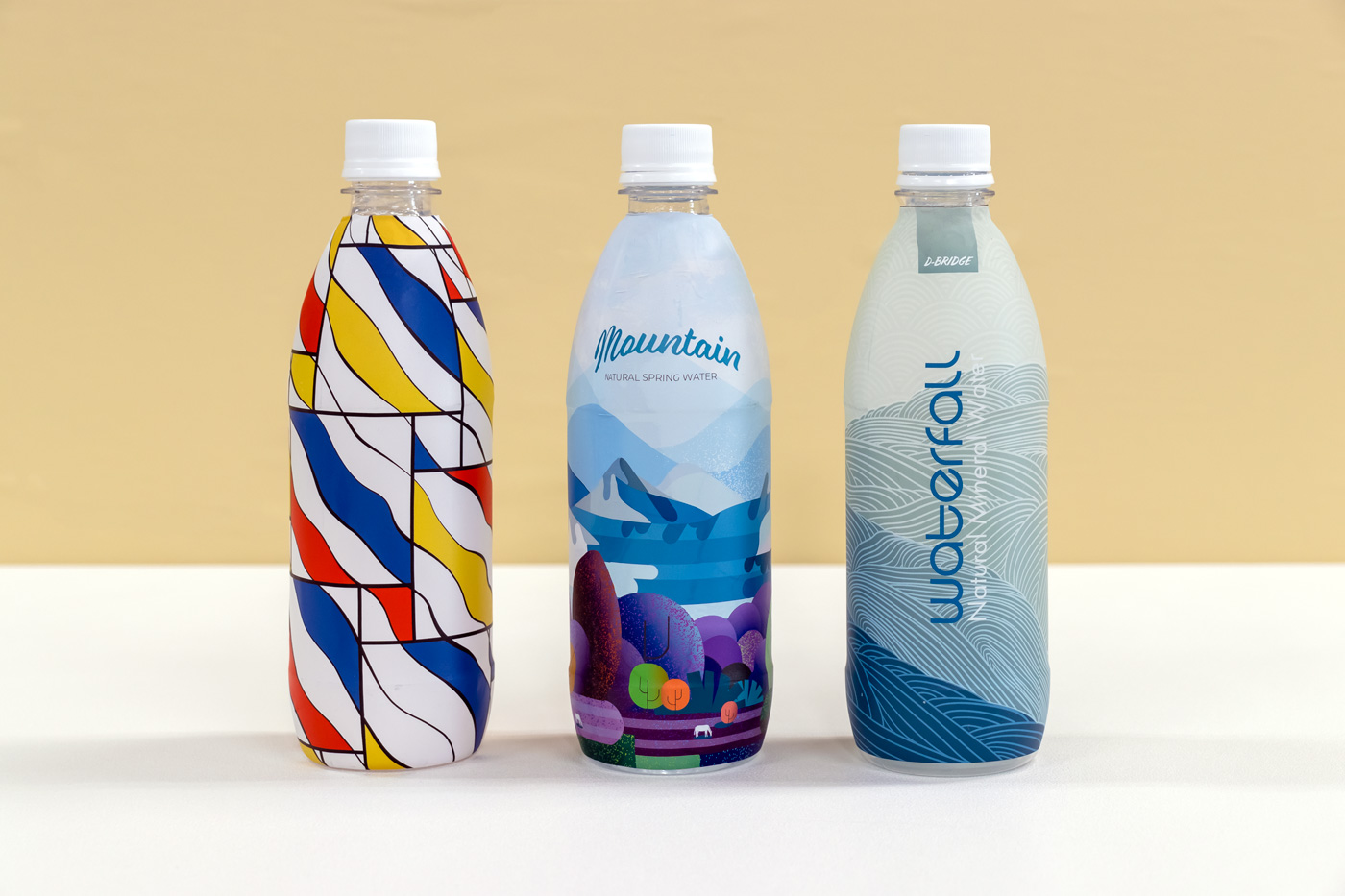
PET Beverage Bottles
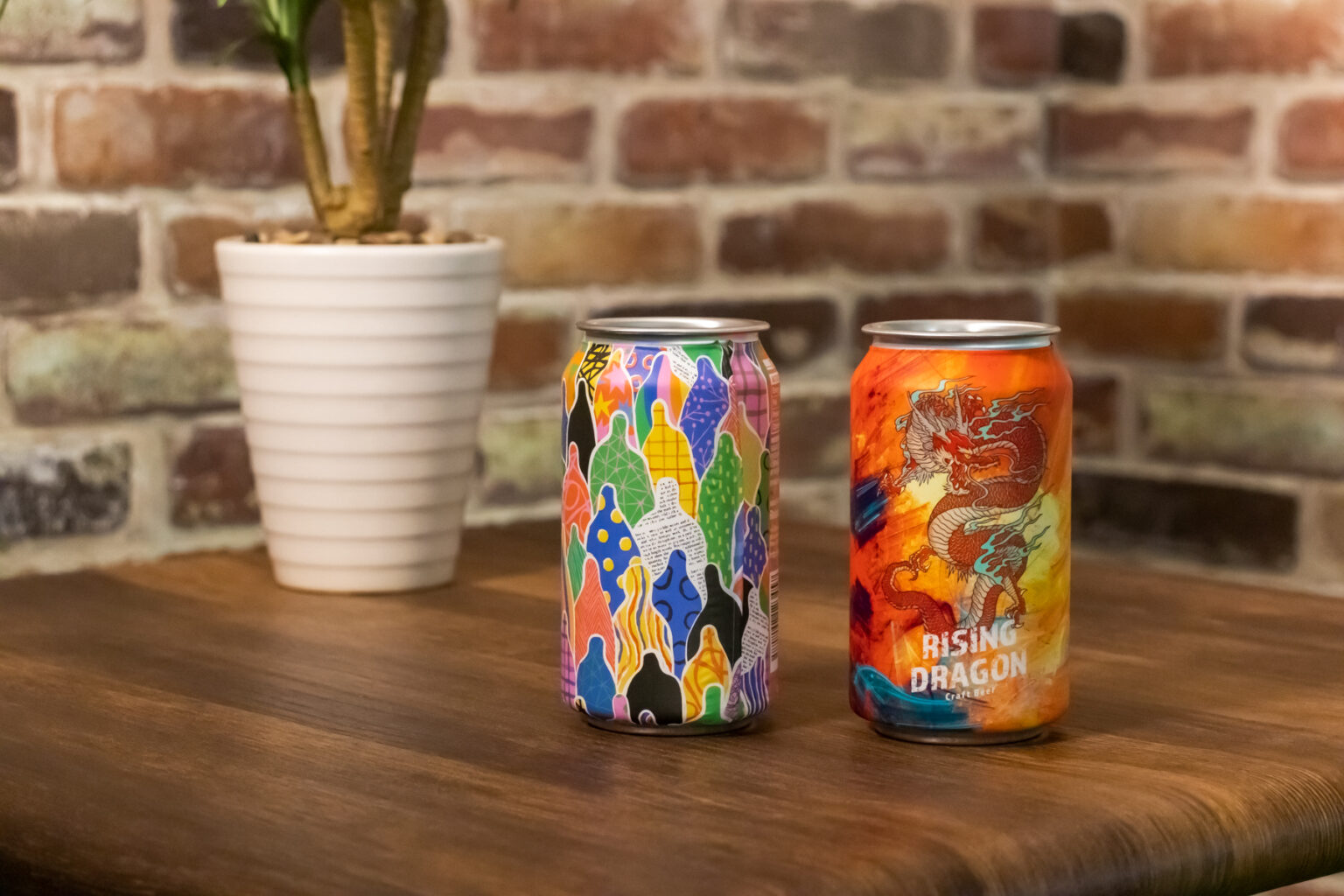
Beverage cans
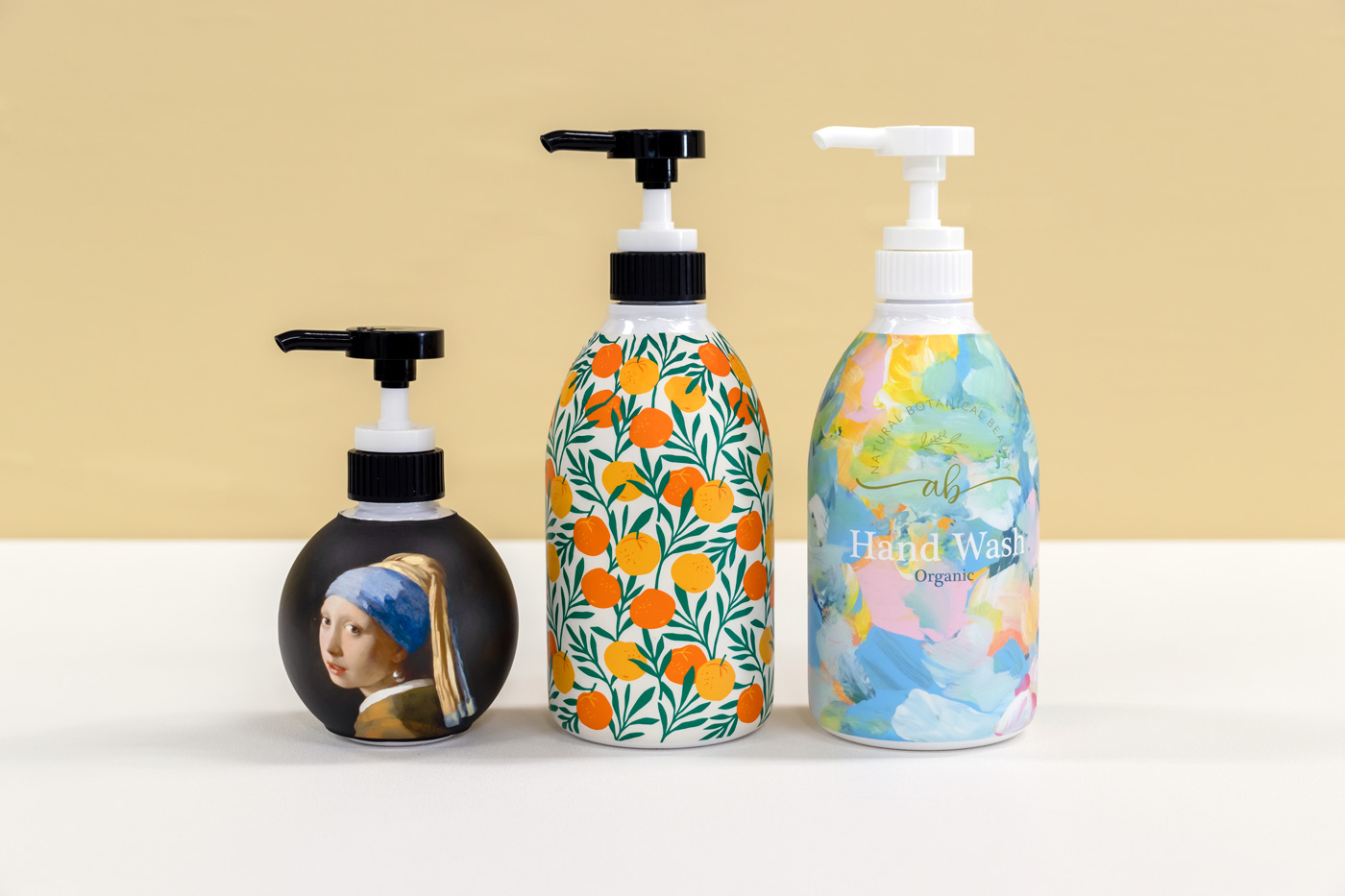
Personal care products
In this article, we will introduce the production workflow for shrink-wrapped mockups using Roland DG's MG-300 UV inkjet printer using ECO-UV S ink which is a superior solution for heat shrinkage. We also used Hybrid Software's iC3D software which is sold by CGS and optimizes design data by simulating heat-induced shrinkage in the production of mock-ups of shrink-wrapped beverage bottles and food products. This combination enables brand owners, designers, package printers, and mock-up producers who design beverage bottles, food packaging, daily necessities, and cosmetics to quickly produce a wide variety of design variations in-house and to support a smooth transition from the design process to the printing and production processes.
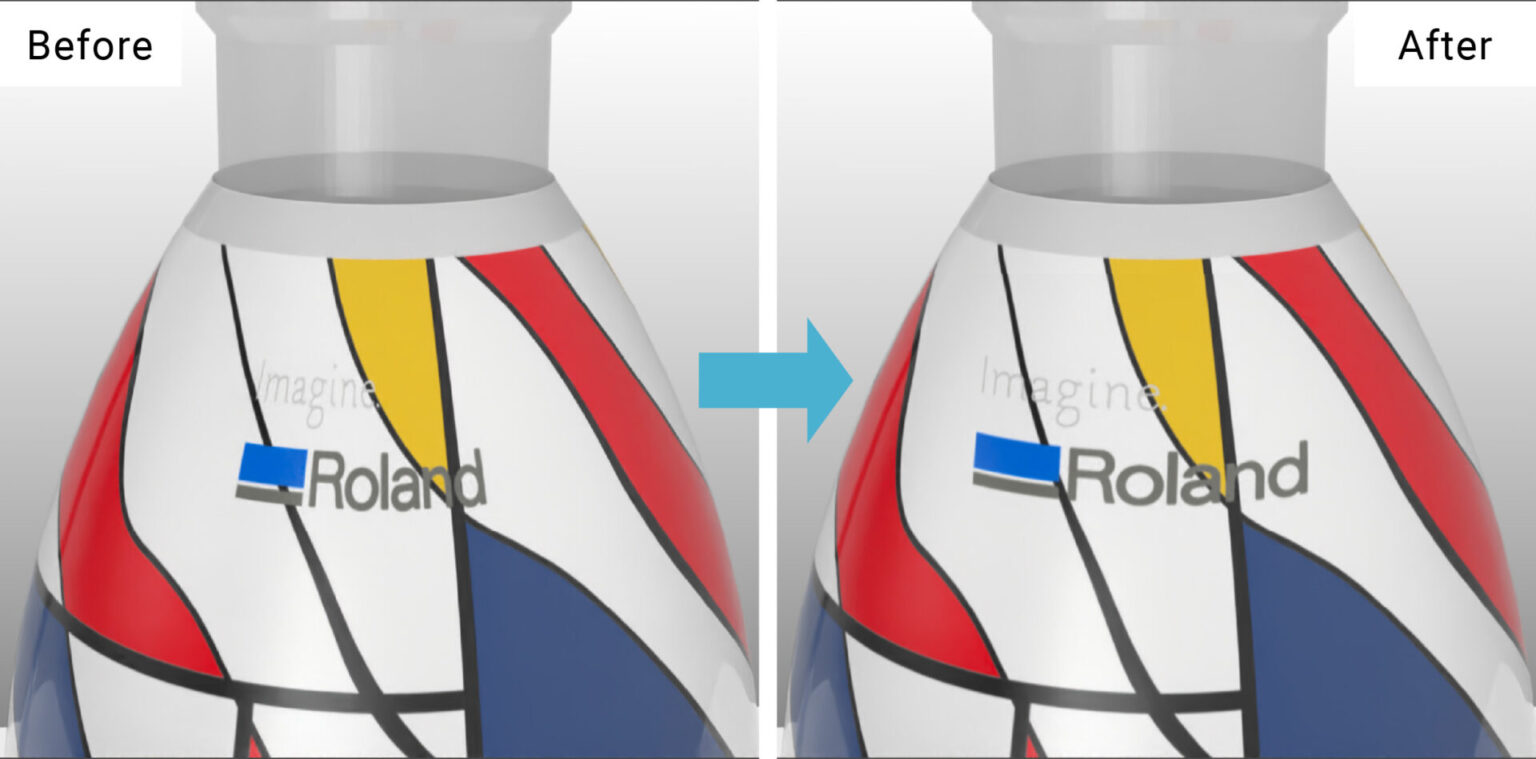
Using iC3D, design changes due to heat shrinkage are simulated in the corrected data (AI file) as reflected in the 3D model of the container.
Using iC3D, design changes due to heat shrinkage are simulated in the corrected data (AI file) as reflected in the 3D model of the container.
What you need
-
VersaUV MG-300 UV inkjet printer with the optional TB-30unit for handling thin films
-
ECO-UV S Inks
-
Design software such as Adobe Illustrator or CorelDRAW
-
iC3D Package Simulation Software
-
Shrink film
-
Hot water tank or heat gun for shrinking film
Production Process
-
STEP1
Preparation of design data
Prepare design data for shrink-wrapping.
-
STEP2
Importing 3D file of container into iC3D
If no 3D file is available, you can create a 3D model of the container in iC3D.
-
STEP3
Simulate shrinkage using design data
Import design data (AI file) into iC3D to compensate for shape changes when shrinking.
-
STEP4
Reflect simulation results in design data (AI file)
Select objects on the design data and apply shrinkage correction.
-
STEP5
Print
Print corrected data on shrink film with the MG-300.
-
STEP6
Wrap printed film around container and apply heat to shrink
Printed shrink film is taped onto a sleeve, attached to a container, and shrink-wrapped using a hot water tank or heat gun.
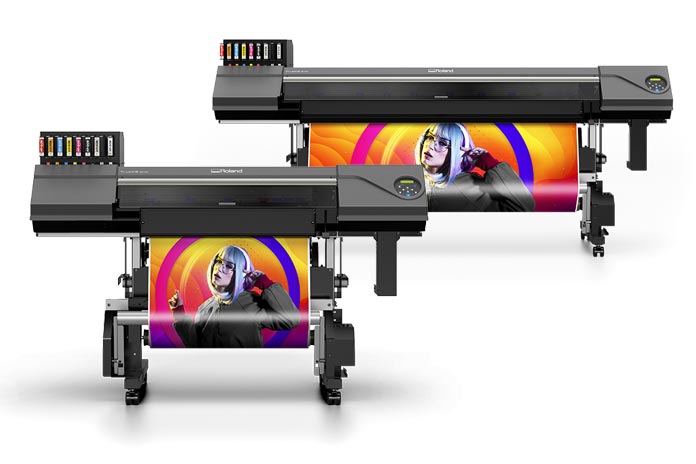
ソリューション事例: Packaging
さらに表示-
Packaging
Mass Customization with Direct-to-object Printing
-
Packaging
Cog’s Secret Methods of Turning Attractive Package Designs into Reality
-
Packaging
How to Quickly Produce a Variety of High-end, Foil-stamped Package Prototypes On Demand
-
Packaging
How to Easily Match Brand Colors with Pantone Specifications